Fraunhofer IKTS and thyssenkrupp nucera have entered a strategic partnership for the industrialization and production of green hydrogen through SOEC (Solid Oxyde Electrolyte Cell) electrolysis technology, producing hydrogen through water electrolysis at very high temperatures. As partners, they combine their strengths for the industrialization of this technology. Ulf Bäumer, Head of SOEC and Service & Digitalization, explains what the partnership and the new technology mean for thyssenkrupp nucera’s portfolio.
The interviewee
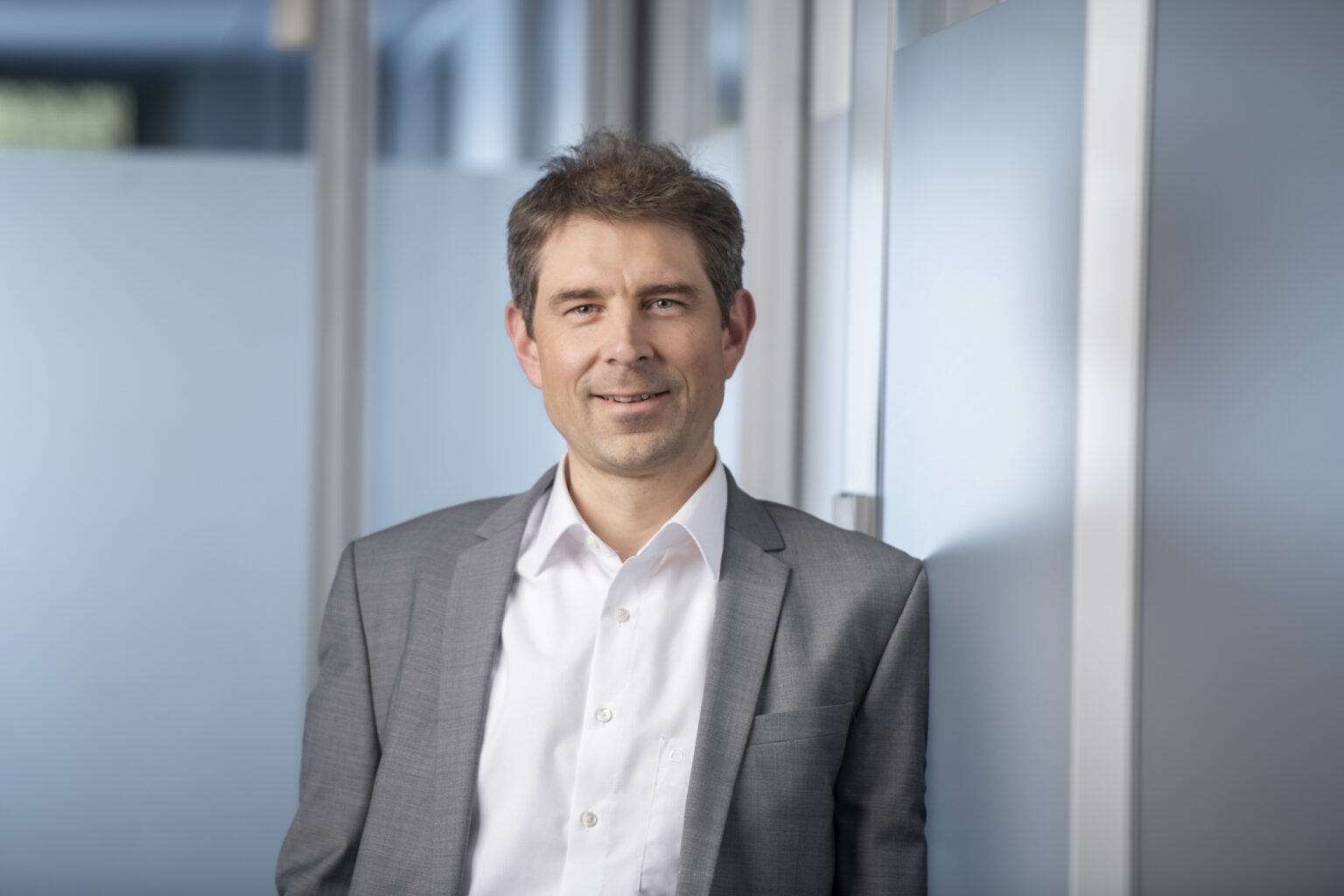
Dr. Ulf Bäumer
Head of SOEC and Service & Digitalization
Dr. Ulf Bäumer, why is thyssenkrupp nucera partnering with Fraunhofer IKTS for SOEC technology?
We have partnered with Fraunhofer IKTS to leverage the promising potential of SOEC technology. Fraunhofer IKTS as a specialist for ceramic technology has been working in the field of SOEC for over 25 years and has extensive expertise along the entire value chain: from material to system, including economic feasibility studies. By now, the basic SOEC research has been completed successfully. To quickly drive forward further work on industrial use, joint forces are needed. Fraunhofer IKTS and thyssenkrupp nucera are two strong partners and a perfect match to leverage the technology.
Why will SOEC be a meaningful addition to thyssenkrupp nucera’s technology portfolio?
Electrolysis is running through our veins: With more than 50 years of experience in electrolysis, chlor-alkali electrolysis is and remains the strong basis for the development of our alkaline water electrolysis technology. We are a leading provider of highly efficient electrolysis technologies and one of the few suppliers worldwide who can produce green hydrogen on a gigawatt scale. Rather than resting on our laurels, we are continuously working on new and innovative solutions. For this reason, we believe SOEC is yet another promising electrolysis technology worth investing in.
Our portfolio technologies thus enable comprehensive sector coupling, i.e. for example the close coupling of the industrial sector with the electricity sector. SOEC will perfectly complement our technology portfolio and offer our customers valuable advantages.
Could you elaborate on the specific advantages?
You can compare SOEC technology to a Swiss army knife – it offers a smart solution for many situations.
If high-temperature electrolysis is implemented in processes in which waste heat is available – such as in the steel industry – a significantly higher level of efficiency is achieved than with PEM and AWE. The efficiency is comparatively very high due to the use of waste heat. The latter converts water into steam, which in turn allows an approximately 30% higher efficiency for electricity to hydrogen conversion. The technology can demonstrate its strengths particularly well with an additional high number of full-load hours and comparatively high energy prices in the region. We expect SOEC to have the lowest cost per kg/H2 in the application areas by 2030.
What are further advantages compared to other water electrolysis technologies?
In contrast to other electrolysis processes, SOEC technology does not require any precious metal components and can also be used in co-electrolysis operation, i.e. the simultaneous electrolysis of steam and CO2, to produce green synthesis gas. The synthesis gas is a gas mixture that can be converted into any hydrocarbon product. Green synthesis gas has the potential to replace crude oil, natural gas and coal as fossil feedstocks and makes a key contribution to achieving climate targets in the industrial and transportation sectors.
Does this mean that SOEC will replace AWE?
No, SOEC will not replace AWE. Our goal is to help shape a new era of clean energy supply with green hydrogen on an industrial scale. We want to achieve this by delivering innovative products and equipment that enable our customers to produce green hydrogen, minimizing their carbon footprint. Both technologies, AWE and SOEC contribute to this goal: AWE is and will remain one of the leading large-scale technologies for producing green hydrogen.
So, are we talking about different application areas for AWE and SOEC?
Not necessarily. With our standardized 20 MW scalum® module, the high volumes of green hydrogen required for industry applications can be produced at low operating costs. AWE is distinguished by its consistent operational reliability and scalability for large-scale projects. SOEC is a different approach and can produce more than 20 percent more hydrogen with the same amount of electrical power, making it attractive for scenarios where thermal energy is available or energy costs shall be reduced.
In the production of hydrogen using SOEC technology, a constant energy supply (steam and electricity) is required to utilize the technology most efficiently. This results in lower flexibility. Therefore, a combination of SOEC and AWE technology is conceivable – SOEC for base load and AWE for alternating load.
What are the main application areas of SOEC technology?
SOEC will be another technology to decarbonize the heavy industry. It enables lower total cost of ownership by its high efficiency when producing green hydrogen and has the ability for co-electrolysis to produce green syngas. SOEC is well suitable for certain applications such as green steel, green ammonia, methanol, fertilizers, and energy storage.
Is SOEC technology already market-ready?
The production of green hydrogen using SOEC technology is currently still taking place in a laboratory environment. This means that we are still at the beginning of the development of high-temperature electrolysis towards industrial-scale use. Therefore, a pilot plant, planned and built by Fraunhofer IKTS, will start operation in the first quarter of 2025. If the preliminary work on the industrial use is successful and financing is in place, we will invest in the development of a large-scale production infrastructure. Experts assume that the market share of SOEC technology could gradually reach around 10% by 2030.