Green hydrogen is a key factor for industry decarbonization and thus the achievement of global climate protection targets. These targets are undoubtedly ambitious, and to come close to reaching them, we need to make hydrogen cost-competitive by implementing larger projects. Alkaline Water Electrolysis (AWE) is a mature technology that can deliver gigawatt (GW) projects already today, because it provides two crucial elements required for the energy transformation: speed and scale. Discover how AWE works, why we have chosen it as our preferred technology, and how we continuously optimize it to ramp up our manufacturing capacity.
Chlor-Alkali leadership as a strong basis for Alkaline Water Electrolysis ramp-up
Our chlor-alkali technology is the DNA for thyssenkrupp nucera’s® Alkaline Water Electrolysis (AWE). Building on extensive experience in large-scale electrolysis, we have applied our proven chlor-alkali electrolysis to industrial-scale green hydrogen production. With a history spanning over 60 years, we have installed more than 10 gigawatts of electrolysis plants and realized 600 electrochemical projects worldwide. Our AWE unit scalum ™ [Hyperlink product page] enables us to deliver the future [hyperlink future solutions page] today and to contribute to the energy transformation.

Today we use energy from renewable sources (such as wind or solar) to split water into hydrogen and oxygen. At the cathode water is transformed into hydrogen. On the anode side hydroxyl ions accumulate which turn into oxygen. But that’s not all: “Of course, there are a lot of know-how and technological expertise required to achieve high current density and efficiency on an industrial scale. Our high-quality cell is leak-proof throughout its entire service life, avoiding emissions at all times. And with ‘zero gap’ over the whole diaphragm area, we improve the separator’s life and performance”, says Jens Kuhlmann, Head of Test Center Water Electrolysis at thyssenkrupp nucera. “Refined hydraulic and fluid dynamics ensure efficiency and longevity, and with a uniform distribution of the electric current, we minimize energy losses. The high-performance coating of our partner Industrie De Nora further optimizes the overall electrochemical process in the cell, as well as the efficiency of the product.”
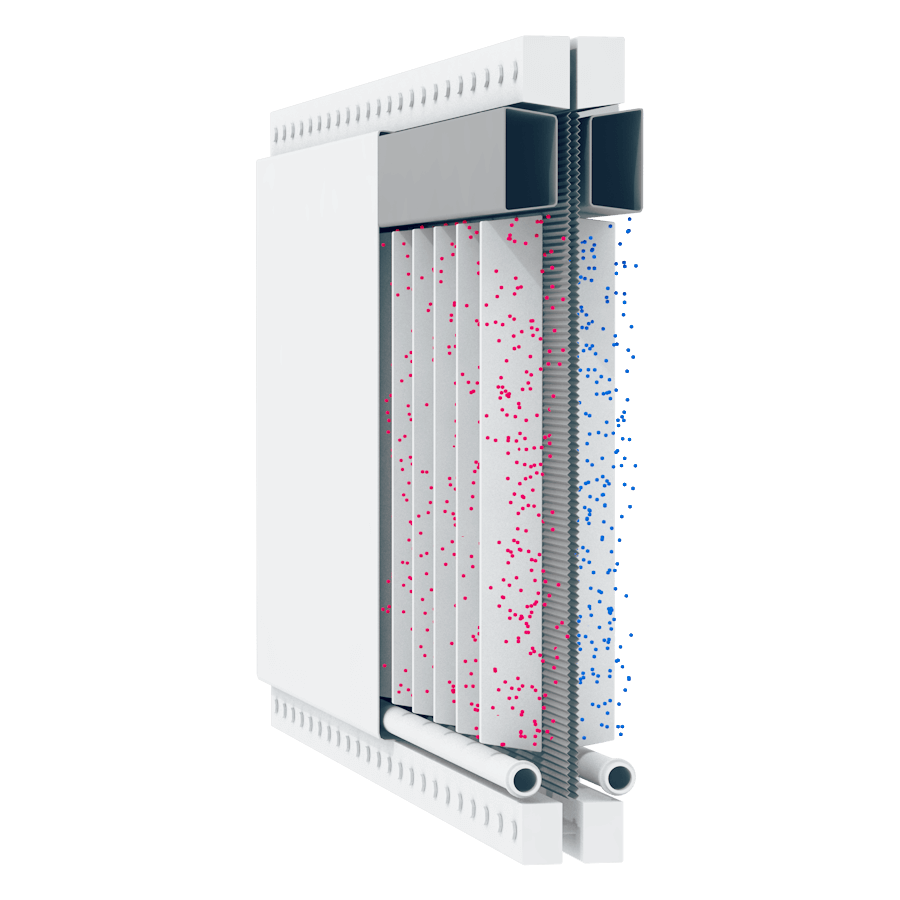
Carbon2Chem test facility: Passionate for innovation and committed to the continuous optimization of our technology
In 2018, thyssenkrupp nucera‘s® 2 MW green hydrogen demonstrator plant started operations at Carbon2Chem in Duisburg. It can run both at permanent full load and with rapidly changing load profiles based on the electricity market for high-quality primary control power, thus simulating the volatile availability of renewable energies. At Carbon2Chem, we continuously test innovative materials and components to further optimize and advance our AWE technology. We have a dedicated product development roadmap aimed at 2nd generation electrolysis design with advanced next generation architecture for improved TCO, towards automatized serial production and supply chain at scale.
“What could be better for a developer like me, to make our technology the standard? That’s why we focus on up-numbering. We combine 74 elements into a rack and 4 racks form a unit. Currently, the capacity is 20 MW per unit,” says Kuhlmann. “But we are working consistently on expanding this and here we test solutions already beyond that.” This includes solutions for some of our biggest projects like NEOM – one of the world’s largest green hydrogen projects with over 2 GW – or the 200 MW facility Hydrogen Holland I in Rotterdam, Netherlands.
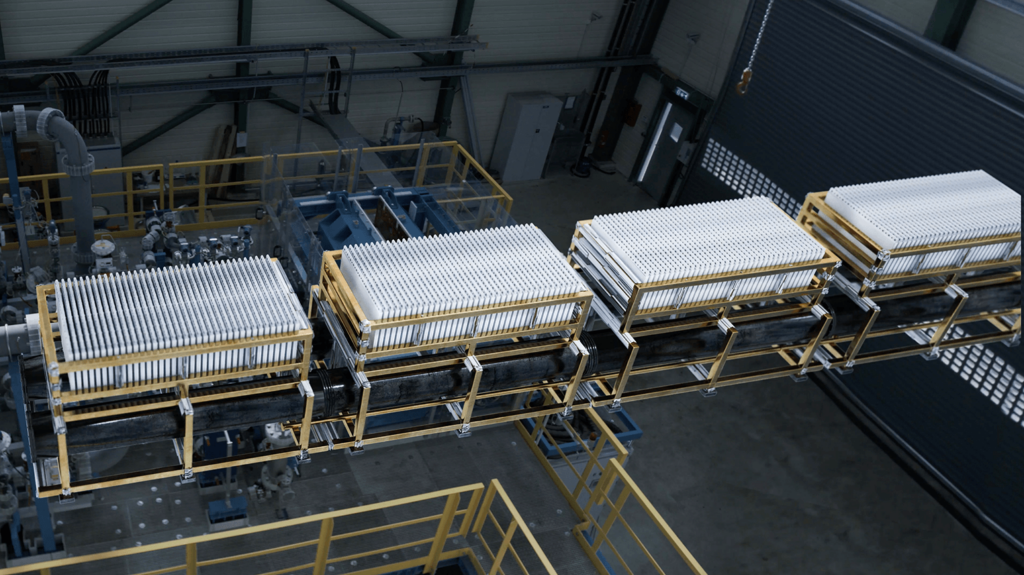
Scale up, number up: energy transformation needs industrial scale solutions
AWE plants with several hundred megawatts or gigawatts of capacity will now be installed more frequently as the ramp-up of hydrogen production plants in carbon-intensive industries is gaining momentum very quickly. Only large installations make hydrogen cost competitive and provide the amounts of hydrogen we need to decarbonize the industry. That’s why our R&D efforts are focused on transitioning our electrolysis business from a customized project business to a mass volume and standardized product business that is fully automatized to deliver high capacities and come down with costs. We already produce at GW scale today and stand by our commitment to increase our manufacturing capacity to 5 GW in 2025. We are well on track to achieve this but we can’t do it alone. Shaping the new era remains a collaborative effort of all players along the entire hydrogen value chain – across sectors and borders.
Embracing an open mindset, fostering collaboration and driving innovation
By engaging more partners, industries, and allies, we strive to transform at a gigawatt scale to help shape a more sustainable future. It is this broad understanding and collective determination that convinces us of our shared success in this endeavor.