Which water electrolysis technologies are available on the market? What do they have in common? How do they differ? Our overview will shed some light on the subject.
In water electrolysis, water molecules are split into their basic components, hydrogen and oxygen, using electricity. If the electricity comes from renewable sources (e.g., wind or solar), green hydrogen is produced (keyword Power-to-X). So far so good. And yet, there are several technologies which can be used to produce (green) hydrogen production. We present an overview of the four main types of water electrolysis technologies and highlight their similarities and differences:
- Alkaline Water Electrolysis (AWE)
- Proton Exchange Membrane Electrolysis (PEM)
- Solid Oxide Electrolysis (SOEC)
- Anion Exchange Membrane Electrolysis (AEM)
Similarities of the four main water electrolysis technologies
Four technologies – a lot of similarities: all of the above-mentioned technologies have their design principle in common. As we saw in the explanations above, the cells of all technologies include an anode and a cathode, as well as a diaphragm, membrane, or electrolyte. The cells are surrounded by a bipolar plate and a current distributor. A cell is included into a zero-gap electrolysis stack, meaning that multiple cells are connected in series. Multiple stacks form an electrolysis stack module, varying from single digit megawatt to double digit megawatt, like thyssenkrupp nucera’s® 20MW scalum® unit. Similarities are clear now. But where do the four technologies differ? Let’s deep dive into the modes of operation to get a better understanding.
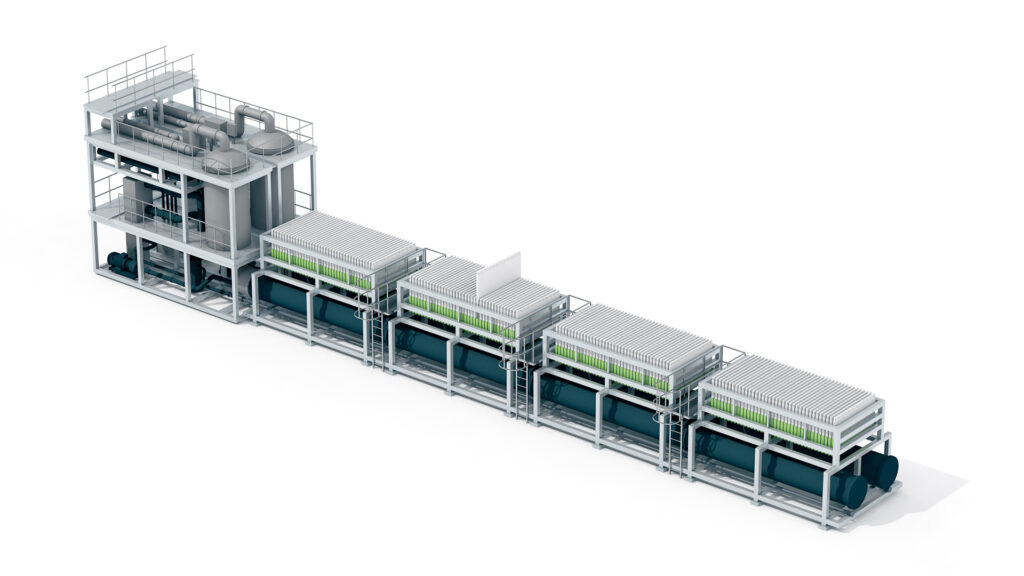
1. Alkaline Water Electrolysis (AWE)
Structure of AWE:
For Alkaline Water Electrolysis, electrodes are immersed in an alkaline solution, usually potassium hydroxide (KOH), which supports the transport of ions, and, thus, the electrolysis process. The electrodes are suspended in half cells that are separated by a permeable, ion-conducting membrane. This membrane is impermeable to gas and thus prevents oxygen and hydrogen from mixing.
AWE process:
At the cathode, electrons react with water, producing hydrogen (H2) and hydroxide ions (OH–).
2H2O + 2e– → H2 + 2OH–
The hydroxide ions can pass the diaphragm, while the hydrogen gas exits the cell. Hydroxide ions react at the anode and form oxygen (O2) and water (H2O), releasing electrons.
2OH → ½O2 + H2O + 2e–
Characteristics of AWE:
- AWE works at high temperatures and high pressure.
- It is characterized by high long-term stability and comparatively low investment costs.
- Currently, AWE systems achieve the highest levels of efficiency.
- AWE is ready for industrial-scale usage.
2. Proton Exchange Membrane Electrolysis (PEM)
Structure of PEM:
In contrast to AWE, PEM works in an acidic environment. PEM electrolyzers do not contain liquid electrolytes, but a solid, acidic proton conducting membrane. It allows protons to pass but blocks electrons. The membrane is thus taking an active role in the ion proton conducting process.
PEM process:
Water is supplied at the anode. With the release of electrons (e–), water is oxidized to oxygen (O2) and hydrogen protons (H+) at the anode.
H2O → ½O2 + 2e– + 2H+
The hydrogen protons pass through the membrane to the cathode. Hydrogen (H2) is reduced at the cathode when they react with electrons (e–).
4H+ + 4e– → 2H2
Characteristics of PEM:
- PEM works at low temperatures and at elevated pressures.
- The technology has been used in science historically and is currently in a scale up phase to industrial use.
3. Solid Oxide Electrolysis (SOEC)
Structure of SOEC:
For SOEC, a solid electrolyte cell is needed, which typically consists of ceramic materials such as yttrium-stabilized zirconia electrolyte (YSZ). The solid electrolyte separates anode and cathode.
SOEC process:
At very high temperatures between 500°C and 1,000°C, water vapor is fed into the cathode. When an electrical voltage is applied, the vapor at the cathode-electrolyte interface is reduced to form hydrogen and oxygen ions.
H2O + 2e– → H2 + O2-
While hydrogen gas leaves the cell at the cathode, the electrolyte enables the transport of oxygen ions (O2-) from the cathode to the anode. At the anode, oxidation takes place. Oxygen ions absorb electrons and form oxygen gas (O2).
O2- → ½O2 + 2e–
Characteristics of SOEC:
- To withstand high temperatures SOEC requires the use of ceramics.
- With high temperatures, the reactions can happen faster which leads to high efficiency.
- The technology is sensitive to temperature fluctuations.
- SOEC was, as PEM, historically used in science, niches and is currently in a demonstration phase for industrial applications.
4. Anion Exchange Membrane (AEM) Electrolysis
Setup of AEM electrolysis:
Anode and cathode are separated by an anion exchange membrane.
AEM process:
Under electric current, water (H2O) soaks the anion exchange membrane and migrates from the anode to the cathode, where it is split into hydrogen (H2) and hydroxide ions (OH–).
2H2O + 2e– → H2 + 2OH–
While the hydrogen gas leaves the cell, hydroxide ions migrate to the anode. At the anode, hydroxide ions and electrons (e–) react to oxygen (O2) and water (H2O).
2OH– → ½O2 + H2O + 2e–
Characteristics of AEM:
- AEM is using alkaline solutions and potentially high current density.
- The technology is currently regarded as in R&D stage.
Closer look reveals differences
The devil is in the detail. Even if the four main water electrolysis technologies have a fundamentally similar structure, the electrolysis process is different. These differences are mainly caused by the required and used materials that enable charge transfer as well as the operating temperature of the technology to split water. The operating conditions and the choice of electrolyte determine the choice of materials.
Which one is the preferred water electrolysis technology, after all?
Each technology has advantages suitable for their respective field of application.
thyssenkrupp nucera® focuses on AWE as it has proven over decades that it is efficient reliable and capable to cope with renewable energies. It is regarded as the most mature technology with an already proven longevity and scalability for industrial scale usage. Find further information on our AWE scalum® here.